Origin
Masahiko Goto began playing saxophone in 1990. He joined a local community band and fell in love with Jazz. He gradually became unsatisfied with standard mass-produced mouthpieces, desiring to play on something of higher quality. The classic vintage mouthpieces held the quality he desired but were not easily obtainable. For that reason, he decided to start creating mouthpieces himself from scratch, and founded “Gottsu” in 2005, which is taken from his own childhood nickname. Since then, he has been dedicated to creating the very best mouthpieces, all for his passion for Jazz.
In 2008 Gottsu released the Sepia Tone line of mouthpieces which quickly became one of Japan’s favorite mouthpieces. In 2014 Gottsu began manufacturing mouthpieces, with the exception of the original Sepia Tone Line, using a CNC machine, combining precision machining with traditional hand-craftsmanship. This led to many of the current Gottsu models, such as the VI, Jazz Soloist, Jazz Metal, and the Master and Double Ring. In 2021, Gottsu began crafting with silver, and released its original silver ligature and “Masahiko Goto” signature VI mouthpiece which had a silver shank ring.
Gottsu's Vision
To make the best saxophone mouthpieces in the world
We believe “music” occurs when musicians share joy with audiences. We wish to support those times with our mouthpieces, so we give our whole hearts to carefully making each and every one of them.
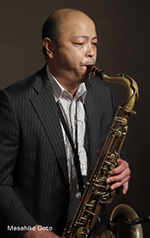
Playing saxophone brings joy not only to players but also to listeners, through beautiful tones and melodies that pull at your emotions. I think those are wonderful moments. My goal will be achieved not simply by making superb mouthpieces but when musicians perform with Gottsu mouthpieces on stage and share joy with their audiences. I am so proud to support those moments with my mouthpieces.
—Masahiko Goto—
Values
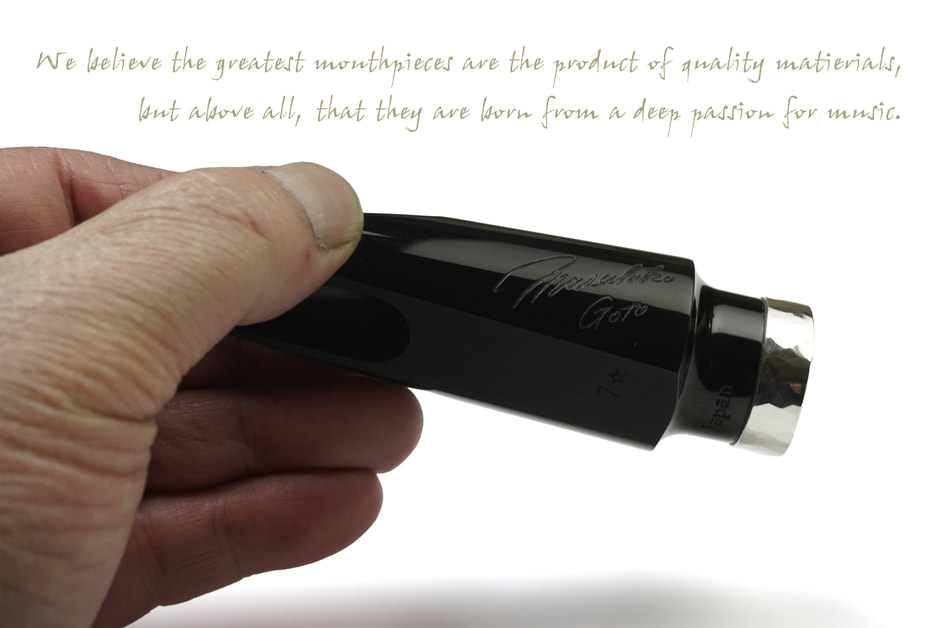
The Mouthpiece Production Process
3D Binaural Recording of Gottsu Mouthpieces
Binaural recording is a method of recording sound that uses two microphones, arranged with the intent to create a 3-D stereo sound sensation for the listener of actually being in the room with the performers or instruments. This effect is often created using a technique known as “dummy head recording”, in which a mannequin head is outfitted with a microphone in each ear. Binaural recording is intended for replay using headphones and will not translate properly over stereo speakers. This idea of a three dimensional or “internal” form of sound has also translated into useful advancement of technology in many things such as stethoscopes creating “in-head” acoustics and IMAX movies being able to create a three dimensional acoustic experience.
We have binaurally recorded each Gottsu mouthpiece in order to give you an accurate representation of what it sounds like. You can find these binaural audio clips in the Products page for each mouthpiece. Please listen with headphones for the best experience.
HL 2018 Tenor | |
VI Custom Bari |
Tip Opening Sizes
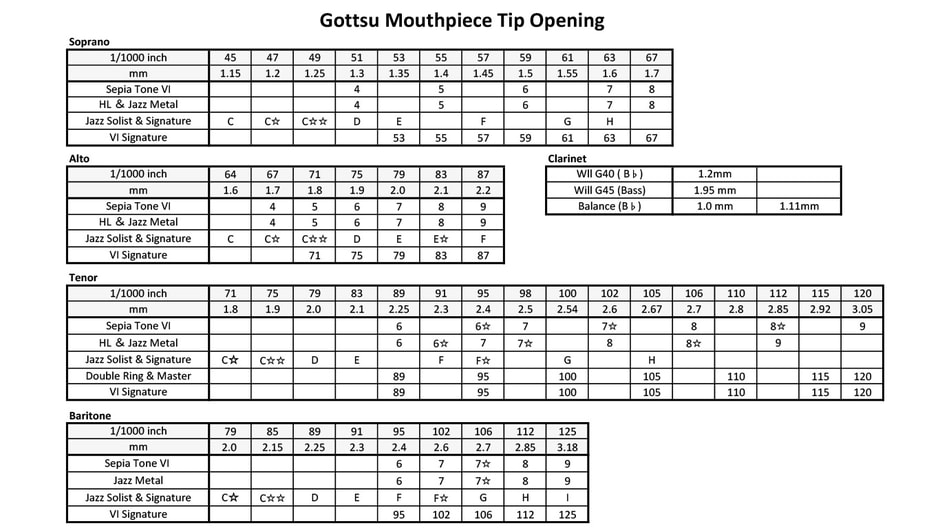